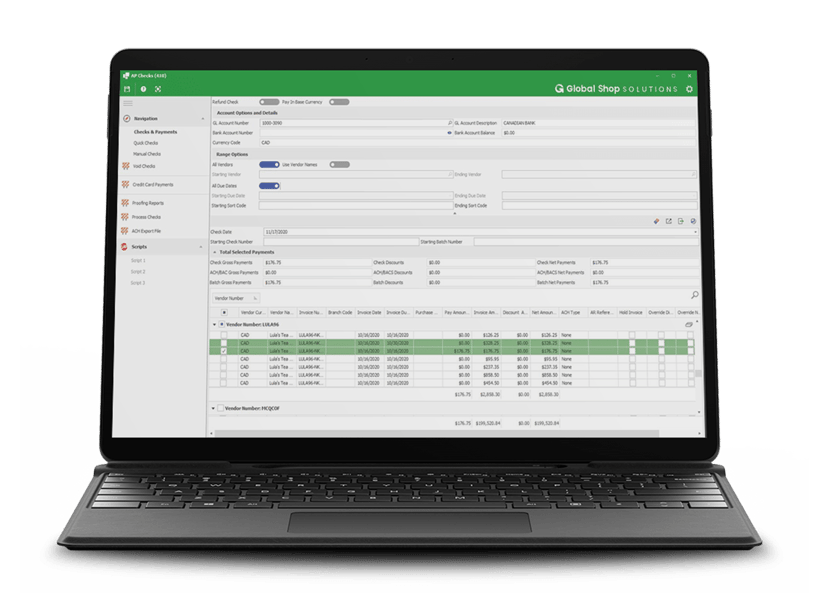
HOW TO COST JOBS MORE ACCURATELY
IS THIS YOU?
Collecting direct labor time is still a handwritten process
Indirect labor costs seem excessive - but nobody knows why
It takes days or weeks to come up with the final cost of a job
Job costing is mostly guesswork due to poor data visibility
Actual costs regularly exceed estimates by more than 10%
You don’t know how much inventory you have or how much it costs
You can’t determine if margins are correct
You lose jobs to competitors who can track their costs in real time
Job costing is a historical rather than real-time process
BE BETTER
Track direct labor down to the penny for each job and job sequence
Identify and eliminate wasteful indirect time
Estimate and quote with precision
Track material costs in real time as jobs move through the production process
Compare actual versus estimated costs while the job is in progress
Know exactly what you have in inventory and what it costs
Ensure margins are correct by knowing your true costs
Easily track and build costs for large projects that take months to complete
Drive cost out of your production process while maintaining margins
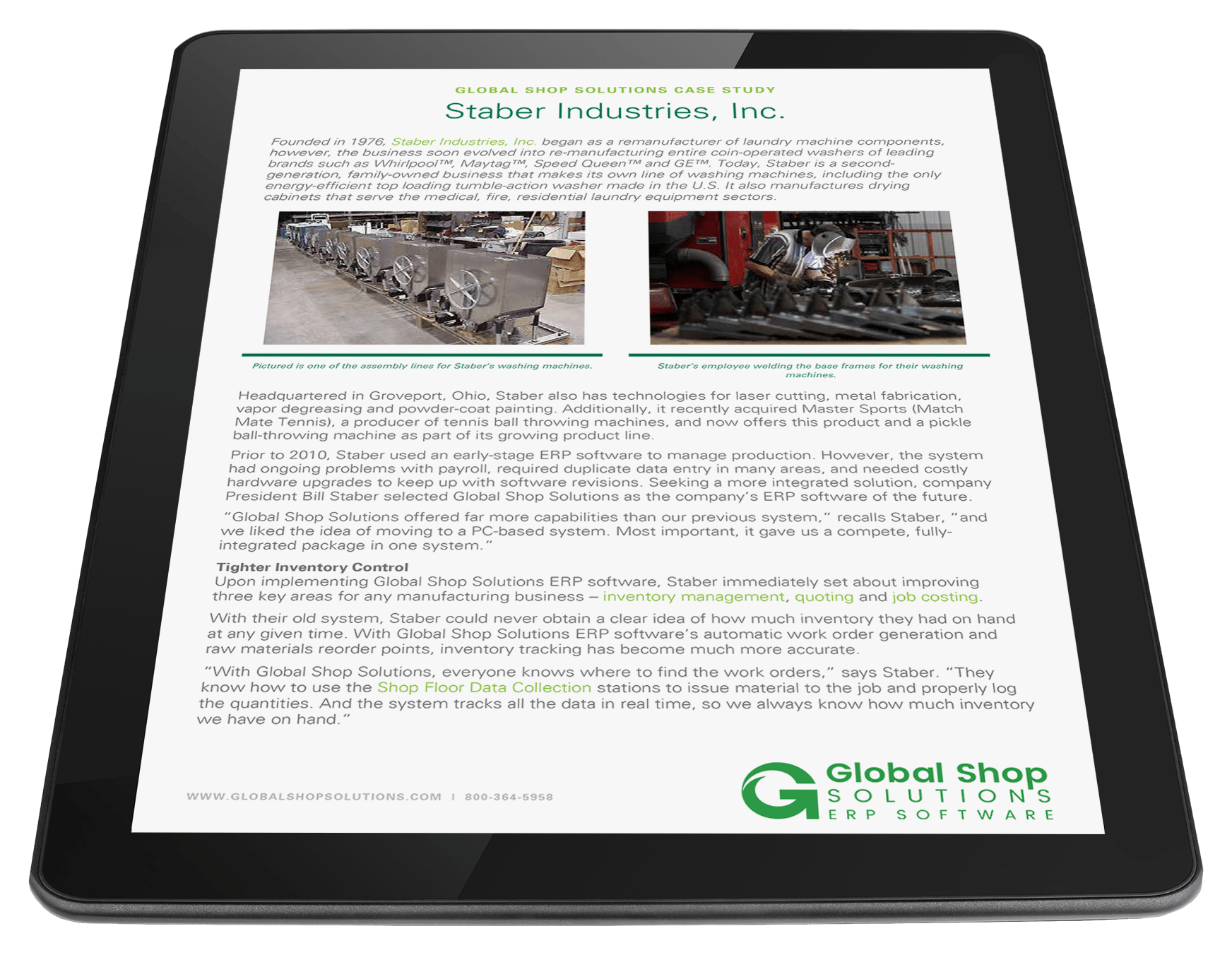
YOU CAN DO IT TOO
Download the case study to read how our customer Staber Industries, Inc. uses precise costing to improve their competitive position.
“Knowing our true costs tells us how much we can come down on price in regards to competitors, and how low we can go before saying no.”
— Staber Industries, Inc.