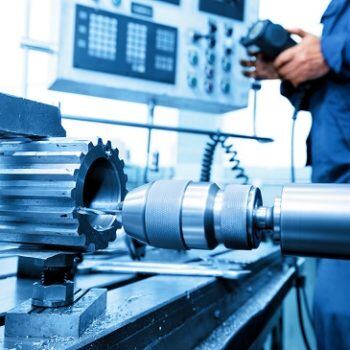
I remember taking long road trips when I was a child and looking out the window to see these massive, monster machines performing incredible tasks – digging, cutting, pulling, moving – you name it, anything with a “ing” these machines can do. As an adult, I am still in awe at these machines and guess what, they are still as massive and monstrous as they have ever been – probably even bigger. These massive machines tell two tales. One tale is what they can do once they are built, but perhaps an even more interesting tale is….how do they get built? Luckily, Global Shop Solutions has been an ERP software provider of choice to machine builders for over 40 years. We have many successful customers that help us tell this story.
Machine builders are responsible for creating a single finished product from sometimes hundreds or even thousands of parts and dozens of materials. Keeping track of all of these parts and materials is difficult enough, let alone tracking all and scheduling all the manufacturing steps needed to build the machine. Our machine building customers tell us one of the most important and critical features of our ERP system that enables their success is bill of materials (BOMs) because it can be entered exactly as it is engineered. This level of BOM accuracy keeps all employees on the same page whether you are looking at your CAD software or the BOM in Global Shop Solutions the data is identical. The BOMs can be created as engineering completes a component of the machine and then added to the parent at any time. This helps save time by not having to create the complete BOM before releasing components for manufacture. How is this so easy in Global Shop Solutions? The answer is simple – our CAD integration plugin for the most popular CAD programs on the market. Designed, developed, and programmed by Global Shop Solutions R&D department ensures compatibility, accuracy, and more importantly – it just works – and doesn’t require a 3rd party add on.
Advanced Planning & Scheduling (APS) for BOMs takes each component and schedules them so they can all come together for the completed assembly. This also allows the manufacturer to see the complete BOM view of the schedule graphically and see issues before they arise. Combining BOMs, APS, and the configurator allows a manufacturer to select the options needed to build the machine, which can help create the BOMs in the system automatically. Another added benefit? This gives information to engineering on how the machine should be configured.
You might be saying to yourself, this sounds pretty easy; what are the challenges? The answer – plenty. We find the majority of machine builders seeking to use Global Shop Solutions ERP software to move from good manufacturing to great manufacturing typically have one or multiple of the following three issues:
- Concurrent engineering – Designing and developing the product can be done in different stages and run simultaneously, saving time and money. The manufacturer can release individual parts or sub-assemblies as those are completed by engineering and then be added to the top level machine at any time during the production process.
- Custom items that must be purchased but don’t want to hold inventory – Global Shop Solutions allows the manufacturer to purchase one off or custom pieces directly to the job without having to create or setup an inventory part. All of the history for this non-inventory item can still be searched and found by the part number, vendor or job it was purchased for and this speeds up the process because it doesn’t clog the database with part numbers that will never have a requirement in the future.
- We do more than manufacture – some machine builders not only sell, but install, lease, and service the finished products they sell. Global Shop Solutions allows a manufacturer to manage all aspects of their product including installation, leasing, and service. Without a fully integrated ERP system like Global Shop Solutions, the manufacturer would have to use separate software or spreadsheets to track these additional processes introducing accuracy and quality concerns in addition to extra cost and training.
As you can see, literally when you look out the window, these monster machines are just as complex to build as they are to use. Luckily, after 40 years of experience Global Shop Solutions is here to help. Want to learn more about how successful our customers are? I invite you to download any of the 150+ case studies available or view our testimonials.