2 min read
Valve Manufacturer Sees 50% Reduction in Time and Paperwork Thanks to ERP Software
Admin September 2, 2020
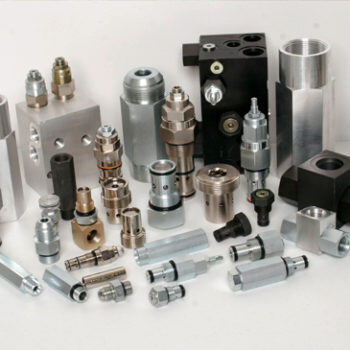
Vonberg Valve, Inc. designs and manufactures custom hydraulic valves for companies in several industries. Specializing in building hydraulic valves for anything that moves vertically, Vonberg’s extensive product line ranges from valves for lift trucks, tailgate lifts, and dock levelers to hydraulic hospital beds, hydraulic power packs, small mobile equipment and even commercial kitchen equipment.
Vonberg previously managed the business with a custom ERP system that lacked the full range of capabilities required for today’s sophisticated manufacturing environments. Seeking a more integrated ERP system, management selected Global Shop Solutions ERP software.
“The lack of integration required a lot of manual data processing,” says Applications Engineering Manager Justin Levon. “We also struggled to get the support we needed because the vendor was a small company, and making changes or upgrades was costly and difficult. Global Shop Solutions offered a robust package with a high degree of flexibility – a key factor due to our make-to-order business model and offered the support we were looking for.”
50% Reduction in Time and Paperwork
In Vonberg’s old system, the process of creating work orders and purchase orders, shipping the parts out, and receiving them back was performed using Word document templates and a lot of paper. With Global Shop Solutions, outside processing is now handled entirely within the system as part of the router. The process gets triggered on the shop floor. The purchase order is generated and compiled, and the parts are sent to the outside supplier. When the parts return they are received directly into the system. If outside processing is the last step on the router, the parts automatically get WIPed into inventory when they are received.
The result? A 50% reduction in the time required to receive outside processing parts and a 50% reduction in production and shipping department paperwork.
Improved Quality Processing, Traceability
Another flaw in Vonberg’s old ERP program was the inability to track rejected materials and other quality issues within the system. Instead, quality had to be manually tracked and managed on spreadsheets and various paper forms.
With Global Shop Solutions, all return material authorizations (RMAs) are now entered in the system and linked directly to the sales order. Rejections and nonconforming material reports are also linked to the purchase orders and work orders. This has resulted in an integrated quality control system where the data can be easily accessed from one central location rather than manual files scattered throughout the plant.
Fast Tracking of WIP Status
In the past, Vonberg had minimal visibility into WIP. Using the Master Schedule Dashboard in the Advanced Planning & Scheduling (APS) module, Levon can now access a treasure trove of data simply by entering a cutoff date.
“Previously, we could tell whether primary and secondary operations were complete, but we didn’t know if a job had been shipped to the outside plater. Now the Dashboard tells me everything about the status of the job and where it is. It saves a lot of phone calls trying to find out the location of a part or a job.”
Justin Levon, Application Engineering Manager at Vonberg Valve, Inc.
Working Smarter Throughout the Shop
Throughout the plant, the ERP software enables people to work smarter and more efficiently by providing access to the data they need when they need it.
Levon regularly accesses the Supply & Demand screen for a quick overview of all jobs due and any that might be past due. The Purchase Order Action Required screen gives the purchasing manager a quick a snapshot of what action may be required due to quantities changing or parts being below reorder points.
To learn more about Vonberg Valve and how ERP improved their business, download the full case study.