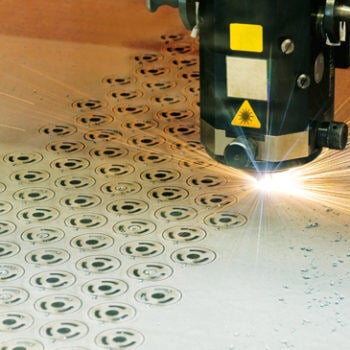
If you laser cut materials, you probably know that nesting software provides an efficient tool for manufacturers to tighten inventory control and reduce waste. For those who aren’t aware, nesting software automatically arranges part shapes on sheets of stock material to produce the least amount of waste. It saves time by eliminating the need to manually plan which parts to cut, and it reduces purchasing costs by minimizing unusable leftover materials.
But if you don’t have a Nesting Interface for your ERP, you’re spending way more time with the nesting process than is necessary.
A Nesting Interface dramatically reduces the time required to nest parts by allowing your ERP system to share information with your nesting software. The nesting software uses this data, such as work orders, inventory information, and workcenter details, to optimize material usage. It then sends cutlist details, material drops, scrap, and estimates for routing and work orders back to your ERP system, providing opportunities to enhance production scheduling, improve estimating and make inventory adjustments. Automating allows employees to focus on making the product rather than moving the data back and forth between the two software.
Recently, one of our customers was manually writing all the material usage/parts after the nest was complete on the floor. The handwritten report was then given to a different person who manually costed time and material. This process was costing them a lot of wasted time and money.
Since implementing the Nesting Interface, the company now exports all open work orders. After the nesting is complete, the operator confirms the time and material directly to the jobs contained in the nest without involving another person or data entry step.
Doing What Nesting Software Can’t Do
Want another example of what a great Nesting Interface can do?
Nesting software can optimize your material usage and reduce scrap, but it can’t determine how much material you have in inventory and how much of it is available for a specific job. You can do both with a Nesting Interface. Your Inventory application tells the nesting software exactly what you have in inventory, down to the exact size and shape. Your nesting software can then identify the best piece to cut that will produce the least amount of scrap.
Our Nesting Interface helps reduce machinist downtime. It can also reduce setup times by running multiple jobs at once and makes it easy to track and use “bone yard” remnants. The Material Consumption feature allows manufacturers that nest multiple work orders together to see available inventory and select which lot to apply to the nest.
Ultimately, a Nesting Interface enforces best practices on the floor with inventory control and operators tracking time/material used. Programmers can nest based on a schedule rather than cherry-picking or having to push work to the laser operators.
What’s New With Nesting Interface
We’re currently developing a new feature for our popular Nesting Interface. It’s called “Inventory Export” and will update your nesting software with the current total full sheets of material you have on hand. This will ensure that programmers using the nesting software out on the floor are always working with the most current inventory data.
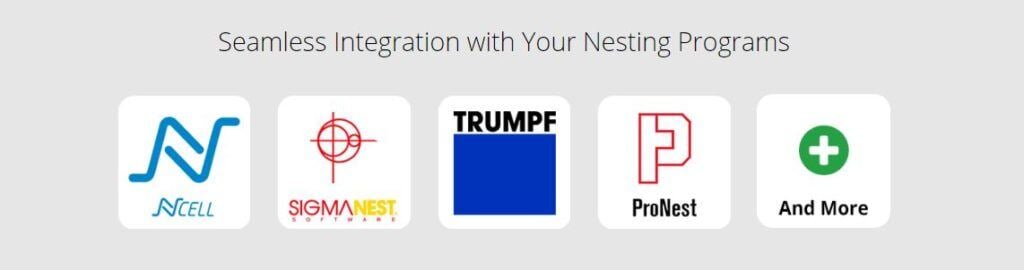
Global Shop Solutions is also working to integrate the interface with more nesting software packages. We currently integrate with SigmaNEST®, Ncell, TRUMPF, ProNest and more.