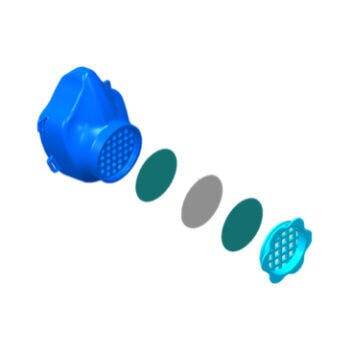
Many companies in the U.S. manufacture and assemble various types of protective face masks, and right now they’re making them as fast as they can. The problem is the foam pads used to cushion the front of the mask and the foam strips used to make disposable shield masks are in short supply.
Milcut, Inc., which fabricates foam, rubber, plastic and high-temperature materials, is doing all it can to help meet the demand. At the urgent request of customers, Milcut began making foam strips for the plastic splash shield that goes on protective face masks. These strips are not one of their standard products. Yet, within three days of receiving the first order, they shipped 15,000 of them.
“The foam strip is similar to products we already make, but we had to make a few adjustments before starting production,” says Curt Huettner, Director of Sales for Milcut. “It’s a fairly simple rectangular strip with an adhesive backing to adhere to the plastic face shield. It’s easy to produce, and we had plenty of foam on hand, so we started cranking them out once we got everything in place.”
Shortly thereafter, Milcut connected with Operation MaskForce, a local effort to bring together companies and resources to produce masks for local hospitals and emergency responders. In this case, Milcut began producing filters for canister masks, a more sophisticated type of protective mask used in hospitals.
“Making the filter was a bit more complex because we had to find a media type that met three essential criteria. It had to be breathable; it had to filter out the correct size particulate (N95 mask goal); and we needed a source that could provide high volume right away. That took us a few weeks to get going, but we’re now supplying them to a local company that makes canister masks.”
Curt Huettner, Director of Sales at Milcut
Production for the filters started at around 1,000 per day, a drop in the bucket based on demand. But Huettner expects Milcut to soon turn out 30,000 per day. Meanwhile, the company is currently shipping around 50,000 foam strips a day to customers throughout the U.S., with total orders of more than 900,000.
“We’re proud to be making front-line components to help prevent the spread of COVID-19,” says Huettner. “This crisis also highlights the importance of having strong supply chains, because we’re all in this together. As long as we can get the supplies we need, we can mass produce the parts. We send them to our fellow manufacturers so they can make the PPEs that end up on the front lines, where they are desperately needed.”
This is just one of our great customers who have risen to meet the challenge. Discover more stories in this multi-part series.