2 min read
Reducing Inventory Counts from Two Months to One Day Made Possible with ERP Software
Admin August 4, 2020
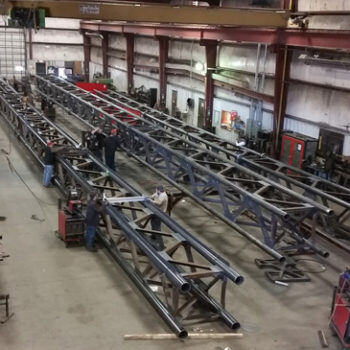
Brookfield Fabricating Corporation is a leading manufacturer of structural steel and aluminum overhead sign structures for use in the commercial, cell tower and highway transportation industries. The three-shop company provides an end-to-end fabrication process for contractors that install sign posts and structures throughout the U.S.
When Brookfield Fabricating’s long-time CEO decided to retire, company management decided it was time to invest in ERP software. After evaluating several different ERP products, they chose Global Shop Solutions.
“Our retiring CEO had a treasure trove of knowledge about the business in his head, and we needed a place to organize and store that invaluable data. We also needed more consistency and accuracy with our inventory, and we wanted to get all the departments working together more effectively. Global Shop Solutions had all the functionality we needed to accomplish these goals in one integrated system.”
Lance Faulkner, Production Control Manager at Brookfield Fabricating Corporation
Count on ERP Software to Reduce Inventory Counts
Before using Global Shop Solutions, physical inventories were performed once a year and involved a considerable amount of labor. After completing the counting, personnel manually transferred hundreds of handwritten pages to a database.
Now, shipping and receiving personnel barcode all incoming materials, which automatically enters them into Global Shop Solutions, where they can be easily tracked as they move through the production process. The yearly inventory count is now conducted with Bluetooth scanners and mobile tablets instead of pencil and paper. What used to take two months now takes just one day with ERP software.
Certification Packets at the Touch of a Button
Most of Brookfield Fabricating’s contract customers are required to submit certification documents for all materials used in their jobs. This, in turn, requires Brookfield Fabricating to put together supply material certification packets, some of which contain 70 pages of certifications, for most of their jobs.
When Brookfield Fabricating receives material or hardware, they scan the certification document and use Document Control™ software to attach it to the material or hardware. As materials get issued to various jobs, the certs remain attached with the job, eliminating the need to spend time searching for them in a file folder somewhere.
Here’s the real payoff: Brookfield Fabricating had a tailored program built (using the Global Application Builder, or GAB) that enables them to pull up a certification checkbox as each job is completed. The checklist shows all the linked documents, and workers simply check off each certification needed for the packet.
The Right Data When and Where People Need It
Meanwhile, company-wide access to data is generating process improvements throughout the business.
- Improved workflow. Production workers can electronically access the work orders to see when issued materials are due to arrive. This allows them to start jobs ahead of time using materials they have on hand. When the ordered material arrives, workers already have part of the job built and ready to go.
- Reduced setup times. Instead of cutting only one or two parts at a time, Brookfield Fabricating now cuts more efficiently and tracks the pieces in their ERP software for use in future jobs reducing setup times by handling the material only once instead of multiple times.
- More accurate labor costing. Workers electronically log on and off all jobs using the Shop Floor Data Collection software on the shop floor, allowing Brookfield Fabricating to determine labor costs down to exact sequence.
“Every morning I get a report showing all the jobs worked on the previous day and what materials were issued," says Faulkner. "If something doesn’t look right, I can talk to the people involved to make sure everything is going to the right place and being worked on at the right time.”
“The Work Order Dashboard provides a quick overview of all the open jobs, including when hardware and materials are coming in and which portions of the job have been completed,” he concludes. “Global Shop Solutions gives us a snapshot of everything going on in all three shops at any given time, allowing us to run our business more efficiently and effectively.”
Download Brookfield Fabricating’s full case study to learn more about how ERP software improved their business.