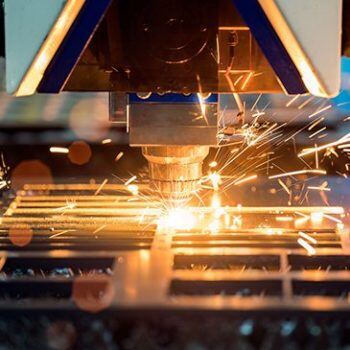
Maintenance. A word that laser machine owners know, but a practice that is often overlooked. Imagine the headache of trying to complete a job on time, only to have your machine down because of something that could have been prevented with routine maintenance. You’ve invested in a good machine and in nesting software to improve shop floor productivity, so it’s crucial to keep these investments in tip-top shape and keep your shop fully optimized.
What, Where and How
Every shop is unique. Shops around the world are using lasers to produce numerous parts, cutting a variety of materials from aluminum to stainless steel. What you’re cutting, where you’re cutting and how you’re cutting should be considered when developing a maintenance plan. It’s important to keep in mind the materials that are being cut, the temperature and cleanliness of the shop and the skill of the operator(s). These variables all impact the wear and tear on the machine. While some machine manufacturer’s offer suggested maintenance programs, here are four simple steps laser cutting machine users should be doing weekly.
- Reset Optics Setting. Out-of-spec optics can adversely affect the cutting quality and optic life. After any work is performed on the machine, it is critical to check that the machine’s settings are restored to the original OEM specifications to avoid these problems. Even better, perform a weekly check to ensure your optics settings are as they should be.
- Check Alignment. It’s a good idea to check the alignment of both inner and outer nozzles. This is not a difficult task, but is often missed. If an operator runs the machine while the nozzles are not aligned, you risk not only poor cut quality and wasted material, but also damage to the machine. It is worth assigning this task to someone to be completed on a weekly basis.
- Look at the Chiller. Temperature is key. New chiller technology makes maintenance even easier, but its still important to make sure condenser coils and filters stay clean. However, if the machine isn’t working on the weekends, the water in the chiller may be more conductive, and it’s important for the operator to run the chiller prior to operating the laser on Monday. If not, the result could be resonator damage- an expensive repair that would cause ample downtime.
- Keep It Clean. It seems like a no-brainer, but keeping the machine clean is critical to good preventative maintenance. The build-up of debris, grease or dust on a machine can have a negative impact on the machine’s performance. For example, build up on the machine’s slats can cause material to shift while cutting, affecting material optimization and overall productivity.
Follow these four simple steps weekly to keep your laser machine fine-tuned and be sure to have a maintenance plan in place that is specific to your shop. Time is money, and fabricators can’t afford to have a machine down. Take precautionary care of your laser cutting machine to keep your shop floor productive.
Looking for ways to fully optimize your laser cutting machine? Visit www.sigmanest.com and request a demo!
Authored by SigmaNest, one of our industry partners.