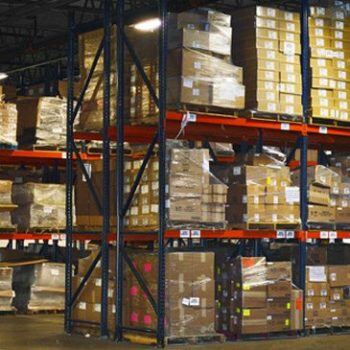
Founded in 1986 and headquartered in New Jersey, the Design Display Group (DDG) is a custom manufacturer of point-of-purchase displays, fixtures and signage, including retail store interactive and freestanding displays, as well as motion light and sound displays. Specializing in high-end displays for cosmetic products, DDG also serves the health and beauty, toys, electronics, apparel and home improvement industries with award-winning displays that help their customers increase brand awareness and sales.
Cutting Way Back on Paper
After acquiring Global Shop Solutions in the early stages of the company’s development, DDG started by training employees to help them understand and use the ERP system more effectively. To ease the transition, management planned a number of quick “wins” to get employees on board with using the system. The first of these involved a dramatic reduction in paper.
“Instead of having people spend hours manually writing and rewriting to document their production, we started using the auto reporting features to tell us how much we produced and shipped at the end of each day,” says DDG Chief Financial Officer John Bollbach. “Once people realized how much time this saved everyone, attitudes about the value of using the system quickly changed.”
20% Reduction in Materials Spending
Next, DDG set about bringing inventory management into the 21st century – a critical process considering the company manages about 15,000 distinct part numbers. Using Global Shop Solutions in the warehouse, DDG has gone from having no real inventory processes (including zero physical inventory counts) to having a sophisticated inventory system that enables management to quickly and accurately access the number, amount, and value of all inventory assets.
“We’re also doing a better job of managing our Kanban inventory. We actually know where to find materials, which speeds up job production. And the visibility of inventory data has reduced material purchasing costs by 20%. Before, we always over-ordered. Now we can see what we have on hand and order only as needed.”
The visibility of inventory data has reduced material purchasing costs by 20%.
John Bollbach, Chief Financial Officer at DDG
Simplifying their Manufacturing
As DDG continues to use more of Global Shop Solutions’ total package, they continue to find new ways to simplify and improve their manufacturing and business processes. Faster order processing, customizable reports, managing customer constraints and improving customer service are all areas in which DDG has improved tremendously.
“Global Shop Solutions provides a complete yet flexible ERP system,” says Bollach. “You can use some or all of the modules based on your needs, and you can create ad hoc reports and other changes to fit the software to your business. DDG has experienced a lot of growth recently, and the system helps us do a much better job of planning our workload. Without it, we probably wouldn’t be where we are now.”
To learn more about Design Display Group and their use of Global Shop Solutions to simplify their manufacturing, download their case study.