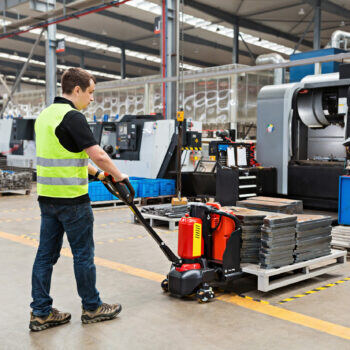
Do you ever find yourself shipping jobs late because parts or materials didn’t arrive on time? Or perhaps accumulating excess inventory because jobs are moved without notifying purchasing?
Shop floor problems like these can be frustrating, but the good news is they can be avoided. Picture the following:
- Data given to purchasing is accurate 100% of the time.
- Lead times are true rather than estimates.
- Buyers are certain that inventory levels are correct.
- Re-order notifications come in real time at the right time.
- Purchasing information is at your fingertips exactly when you need it.
All of this is possible through your ERP software.
How much time and money would that save your business? How much more competitive could you be? How many happier customers would you have?
To make smarter purchasing decisions and modernize your manufacturing purchasing process, download the 5 Ways to Modernize Your Manufacturing Purchasing whitepaper. This whitepaper will give you 5 ways to simplify and bring your purchasing process into the 21st century – with the right ERP software, of course.
Long-time customer and metal fabricator DeJong Manufacturing modernized their purchasing and found great success.
“When one of my commodities hits the reorder point, Global Shop Solutions automatically notifies me through the message system without my having to run the auto purchase report. If I’m traveling, it sends an email to my phone, telling me the quantity and type of commodity I need to order. All I have to do is message a team member to order the materials so they arrive in time for the job.”
Matt DeJong, Vice President of Sales and Manufacturing at DeJong Manufacturing, Inc.
Read DeJong Manufacturing’s full case study here.
By bringing your purchasing process into the 21st century, you’ll find ways to make your buyers’ days easier, your bottom line in the green, and your customers happier.
Download the 5 Ways to Modernize Your Manufacturing Purchasing whitepaper to start your journey today.