2 min read
Gear Manufacturer Achieves Award-Winning Delivery Times with ERP Software
Admin November 12, 2019
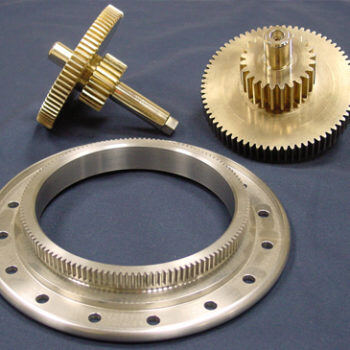
Bendon Gear & Machine, Inc. specializes in the production of precision-machined components, custom precision gears, mechanical assemblies, and gear assemblies that are supplied to the aerospace, naval, and high-tech markets in both prototype and production quantities.
For years, Bendon Gear operated the business with a custom-programmed production management program, various spreadsheets and a stand-alone accounting software program. When this approach became too unwieldy, management sought a more sophisticated ERP system and found it in Global Shop Solutions.
We looked at many different systems, but Global Shop Solutions stood out for its robust capabilities and its flexibility in terms of being able to tailor the different applications to our needs. We also liked the Task application, which allows us to see at any given time who has an order and where it stands in the production process.
Eric Tressel, QA Manager & Systems Administrator at Bendon Gear
Better Manufacturing Communication Through Single-Entry Data
Prior to implementing Global Shop Solutions, all purchasing, job costing and other production data had to be manually entered into the accounting program to manage the financial side of the business. Now, the data only
gets entered once, and Bendon Gear can process all aspects of a job in one integrated system. The result is a leaner, more organized production process where people work together more efficiently.
Effectively Managing Shop Floor Changes
Bendon Gear is often called upon to perform just-in-time work – a process made more difficult by the fact that individual jobs can be in five different areas of the shop floor at one time.
Tracking the status of complex jobs used to require a lot of time and legwork. Now production personnel can instantly determine the location and status of any job through the Shop Floor Data Collection stations located on the shop floor.
Inventory management and accuracy have improved as well, leading to more accurate inventory counts and improved customer service.
Award-Winning Delivery Scores Due to Simplified Document Control
Most of Bendon Gear’s jobs require certification documents and complete traceability of materials, as well as some type of outside finishing process. Bendon Gear simplifies these processes by using the Document Control application to electronically link documents to jobs, work orders, and purchase orders for outside processing vendors.
“Document Control helps to ensure that all the proper certifications are attached to each job,” says company President Peter Belezos. “It also saves time because we no longer have to hunt down the paperwork.”
In the past, Bendon ran the risk of this important documentation being left out of a shipment. Now, shippers can tell at a glance if the requisite paperwork has been attached to each shipment. As a result, the company has maintained customer ratings of 100% for excellent delivery, which helped it earn an award from one of its biggest customers.
A Complete Business Management Solution
Customer Liason Marilyn Werkheiser uses the order entry application to see which jobs are coming due in the weeks ahead and proactively address any concerns before the customer calls her. Tressel uses the software to perform the daily balancing and review all job records from the previous day to make sure everything is correct. He also uses the Supply & Demand screen to maintain the cost of parts that have just been sent from work in process to finished goods.
“Global Shop Solutions has transformed our company by giving us access to information we didn’t have in the past,” Belezos says. “The interconnected applications provide superb visibility of the entire supply chain and will tighten up your supply chain as well as your lead times and on-time deliveries. It’s an outstanding supply chain software solution.”
Download Bendon Gear’s full case study and discover all the ways ERP software improved their business.