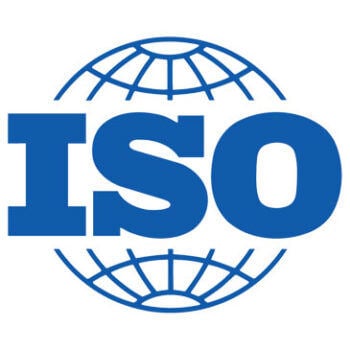
Is it possible to get a complete, fully integrated enterprise resource planning (ERP) software package where the whole process is ISO and QS-9000 compliant? They’re some ERP systems out there that do this, and through them you can achieve the sort of compliance levels you need to document and exhibit ISO and QS-9000. Or, rather, you should be able to do so.
ISO certification requires documenting what you do and proving that you do what you document. Some ERP software has complete traceability including lot, heat and serial number for getting a real edge on quality audits. You can also catch non-performance before it really starts on designated screens in real-time or on each day’s early morning reports.
Of course, impeccable quality always enhances your value to the customer and often means added sales. Scrap costs are reduced through real-time employee reporting, as well as vendor, part and other analysis. With ERP software, you gain considerable advantage over these issues when compared to most non-ERP operations.
With ERP software oversight and documentation, quality means a lot more than just finding and fixing bad parts. It means easy ISO and QS-9000 certification. It also means lower quality costs from accountability by employee, vendor and other defect originations. ERP software makes it easy to qualify for and maintain ISO and QS-9000 certifications by automatically documenting everything you do on the shop floor. The system provides precise, highly accurate data trails. It makes ISO audits easier and more efficient. Ultimately, it allows you to be fully compliant, giving your company a distinct edge in the global marketplace.
ERP software systems should also provide complete traceability of every part or material that comes through your door. Suppose a vendor notifies you of a problem with a part they shipped, putting your customers at risk. With a robust and accurate system, you can enter the heat number into the system and instantly know every part, work order and customer on which the part was used. More important, you can instantly determine the status of all work orders involving the part, allowing you to stop work in progress, postpone shipment, or notify customers that there may be an issue.
Through all of this, ERP software can help you find and fix non-conforming parts, with powerful features such as:
- Non-conforming alerts. When an operator on the shop floor records a non-conforming part, your ERP system instantly notifies the shop foreman, in-process inspector and other selected personnel. One click of the mouse should then tell you everything you need to know about the part — work order, number of pieces, workstation, employee and customer. It can also tell you the value of the part so you can determine the cost of the non-conformance and take appropriate action.
- Customizable reporting. Need to know your biggest reported defect type? Or, the most costly? A built-in non-conforming part report will automatically list all reported defects, sorted by part number, machine number, operator, defect code or other criteria of your choosing, including dollar amount. In addition, the non-conforming materials report tracks when and why vendor materials fail to meet your specifications. Really, quality control for manufacturers has never been as easy as it is today via ERP system tools.
- Multiple tracking options. With ERP, you should be able to rapidly track by lot, bin or heat number for total control over every part that comes in your front door and goes out the back. If a customer work order requires serialization, the system automatically applies it to every document that goes through the shop, from initial work order through final invoice. It also gives you instant access to every transaction involving that product throughout the entire plant.
- Statistical analysis tools. Some of the best ERP systems have built-in statistical analysis tools to allow you to make better management decisions. Suppose, for example, the non-conforming parts report identifies 50 parts with a hole in the wrong location. When you run the report by dollar value, it shows the 50 parts with a total value of $150. The report also lists a defect with only three pieces, but those pieces are valued at $1,200 each. Which job do you think would get your immediate attention?