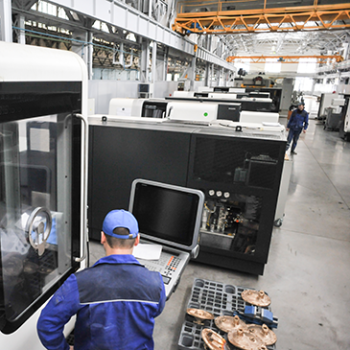
These famous words of Benjamin Franklin ring true in the manufacturing world. There are many ways you can “prepare” in manufacturing, and one of those ways is estimating. Many of the unsung heroes in a manufacturing business are the production, scheduling, purchasing, and quoting employees that are responsible for estimating projects. These unsung heroes have great influence of the profitability, margin, and cash flow of a manufacturer. The more accurate they can be the better it is for every aspect of the business. This accuracy relies heavily on the tools they have at their disposal – mainly their ERP software.
Typically speaking, manufacturers that discover issues with their estimating and production can tie it back to one or all of the following three issues:
- Inaccurate costs – Can be defined as production runs that lose money/margin or have varying costs for the same product when freight, labor, outside services, other costs, and material (FLOOOM) aren’t changing. How do you solve this? Be sure your estimating and the system supporting your estimating allows for a buildup of cost estimates. Also you can review your job costing by the FLOOOM cost components to see where any deviation occurs.
- Poor purchasing – You often find yourself without the raw goods needed to make parts or sometimes even worse, excess raw goods. Schedules get impacted because of material availability and profit, margin, and cash flow gets impacted because of under/over purchasing and poor pricing on raw goods. You want cash in the bank, not in raw goods on the shop floor. How do you solve this? Accurate estimates will drive correct purchasing requirements (and leverage automated purchasing in your ERP software) which will improve cash flow, reduce waste and scrap, and improve on time production and delivery. In the end, delivering a quality part on time, every time will delight your customers and increase sales.
- Inaccurate schedule – You often find yourself explaining to customers that products are shipping late or you find yourself paying employees expensive overtime to meet delivery dates. These are all signs of an inaccurate schedule and lack of flexibility on your shop floor. Accurate estimating will help to straighten out your production schedule maximizing your workforce and machine capacity.
If you find yourself struggling with any of the above it may be an issue with tools more than people. An integrated ERP software system will allow your business to be proactive, improve visibility, and make smarter decisions sooner instead of finding out when it is too late. If your ERP software isn’t fully integrated, you may want to look at it again.