1 min read
ERP Software Brought 22% Improvement in On-Time Delivery in Wisconsin
Admin April 11, 2017
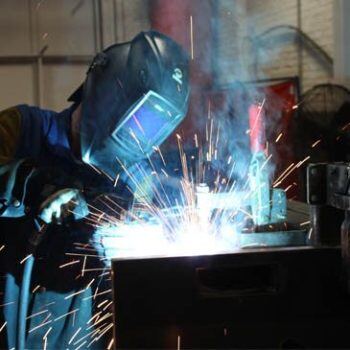
Jensen Metal Products, Inc. (JMP) is a one-stop job shop specializing in contract manufacturing of custom parts and components. Headquartered in Racine, Wisconsin, the company makes everything from complex bracketry and weldments to fabricated assemblies, gaskets, panels, shims, stainless steel glamor parts and more. Currently focusing on the agriculture, oil and gas and lighting industries, JMP serves a diverse clientele from small, privately-owned OEM businesses to Fortune 500 companies.
Like many manufacturers, JMP outgrew its first ERP software. Slow and difficult to navigate, the system suffered from poor data integration and lacked sufficient job costing and scheduling capabilities – two critical areas for custom job shops. Seeking a more robust ERP system that could grow with the company, management turned to Global Shop Solutions.
A large percentage of JMP’s jobs require short lead times and quick turnaround delivery dates, therefore their scheduling process is extremely important. Thankfully, Global Shop Solutions had just what they needed to succeed.
Using the Shop Floor Data Collection software and Advanced Planning and Scheduling (APS), we can track up-to-the-minute data on every job on the shop floor. This allows us to make more accurate scheduling decisions to finish jobs on time and keep our customers happy.
Jeff Lowman, Engineering and Quality Assurance Manager at Jensen Metal Products, Inc.
Previously, JMP lacked the ability to accurately track the production metrics that contribute most to on-time deliveries. Tracking workflow through Global Shop Solutions has also allowed JMP to improve on-time delivery by 22%. The ability to track every step of the production process has led to a significant turnaround.
“Global Shop Solutions gives us a complete – and truthful – picture of what’s happening on the shop floor,” says Lowman. “Between APS and the dashboard we use to track on-time delivery, we can see the status of all open jobs and react to any problems in real time.”
To learn more about how Global Shop Solutions increased success at JMP download their case study here.