2 min read
Eilers Machine & Welding Celebrates 40 Years of Manufacturing Excellence
Admin July 1, 2023
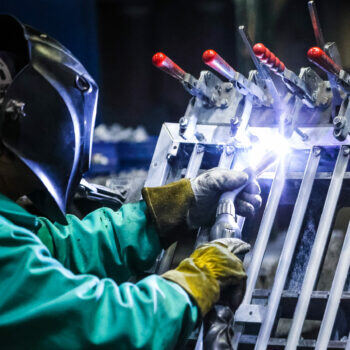
In 1983, Brian Eilers bought a local machine shop and began manufacturing products for the farming industry. Forty years later, the family owned and operated company has evolved into a world-class supplier of close-tolerance fabricated metal products through cutting-edge equipment and technology. Recognized specialists in precision metal fabrication, Eilers Machine & Welding (EMW) currently fulfills thousands of contracts with the U.S. government each year while continuing to serve local farmers and the agricultural community with multiple product lines.
“We are proud to celebrate our 40th year of meeting a broad range of machining, fabrication, welding and finishing needs while ensuring total compliance with customer specifications and tolerances,” says Chase Eilers, second-generation President and owner of EMW. “From close-tolerance, precision-made components for military vehicles to agricultural combine parts, we can take any drawing and turn it into a precision made piece for new or existing customers.”
EMW has developed its 40-year track record by delivering high-quality products that build long-term relationships with their customers. Two of their products – the 610 Track Closer, which repairs soil ruts and tracks at the end of a growing season, and the Gopher Killer, which eliminates gophers without damaging the soil – are must-have tools for farmers. EMW is currently developing the Defender 200, a new agricultural product designed to knock down cornstalk stubble in the field after harvest so it doesn’t puncture tractor tires.
The DOOSAN DNM 750L/50 II, one of the many machines used to manufacture precision made parts at Eilers Machine & Welding’s headquarters in Lexington, Nebraska.
Like most manufacturers, EMW has experienced a number of market fluctuations due to internal and external factors, the most recent being a downturn in the government contracts market due to significant budget cuts. The company persevered and is once again enjoying steady growth thanks to diversifying their product lines, an upsurge in government contracts, and upgrading their business management system to Global Shop Solutions ERP software.
Since implementing the all-in-one ERP system in 2012, EMW has generated tremendous increases in productivity and efficiency while improving product quality and on-time delivery rates. According to Laurie Lira, EMW Controller, the ERP software has simplified the company’s manufacturing by automating most of the scheduling process, tracking inventory and material movements with remarkable accuracy, and eliminating most of the company’s manual data entry. It also tracks production data in real time so managers always know the status of jobs in progress and when they will be complete.
“The time savings with Global Shop Solutions have been tremendous,” says Lira. “Previously we manually tracked all job data on Excel spreadsheets, a time-consuming and error-prone process. Now the data is automatically tracked in our ERP system. Everything we need to know is right there at our fingertips so we can access the entire history of a job with just a few keystrokes.”
With manufacturing markets becoming more competitive, EMW plans to continue expanding into new markets while serving its existing customers with quality products. To achieve this goal the company continually invests in cutting-edge machinery and equipment, recently purchasing one of the newest and fastest laser cutters on the market. EMW’s state-of-the-art mills provide some of the highest and tightest tolerances available, and the company wins many of their government contracts in large part due to the state-of-the art quality system that meets and surpasses all government inspections.
“We learned an important lesson from Global Shop Solutions – don’t let your business get stagnant,” says Eilers. “They constantly update their ERP software with new features and capabilities to help their customers keep up with new technologies. We constantly invest in new machinery and technologies to improve our manufacturing processes and provide our customers with better service.
“For example, we’re currently looking at building a highly automated paint line that will blast the parts and paint them to deliver perfect parts,” he adds. “We’ve had a lot of success over the last 40 years, but we feel the best is yet to come.”