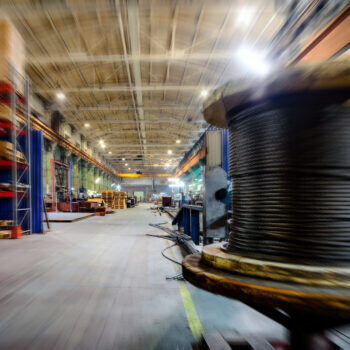
If everything went off without a hitch in manufacturing, life would be much simpler for those who make the products that are essential to our lives. Of course, nothing goes off without a hitch, but facing the challenges head-on can develop new ideas, improve problem solving skills, and lead to better products, more efficient processes, and a higher ROI. This year certainly has its share of challenges. Here are five you would do well to put on your to-do list, with some interesting ways to resolve them.
1. Shop floor labor shortages.
The manufacturing labor shortage has abated in some areas, but the industry is a long way from resolving it. During the first trimester of 2023, the U.S. manufacturing industry totaled approximately 686,000 unfilled jobs. Based on a study, the National Association of Manufacturers is forecasting up to 2.1 million unfilled jobs by 2030. The largest number of unfilled positions range from assemblers, fabricators, and first line supervisors to welders, cutters, machinists and industrial machinist mechanics.
To cope with the difficulty of hiring enough workers, many manufacturers are deploying alternative strategies besides recruiting employees:
- Automating processes to reduce the need for manual labor
- Offering internship, training and certification programs to encourage careers in manufacturing
- Collaborating with local educational institutions to encourage and educate students about the benefits of manufacturing careers
- Creating collaborative partnerships with American veterans to provide manufacturing career opportunities
Automation is the most practical way of addressing labor shortages, and it’s where the industry is headed. Processes can be completed faster, lowering labor costs and improving efficiency. However, don’t overlook non-traditional ways to attract qualified people to manufacturing. The time has come to put creativity to work in solving the shop floor labor crunch.
2. Shortage of financial experts.
At Global Shop Solutions, we see many of our customers struggling with personnel shortages in finance. Their CFOs and other financial professionals are retiring or moving on and it’s hard to find replacements with experience in the company’s ERP system. Further, they may not have the skills required to complete the month end financials in a timely manner. It takes some companies four-to-five months to complete their financial statements, and longer to hire the qualified people they need.
To help these customers resolve their financial hiring problems, we provide a consulting service, Virtual Controller, that produces their monthly statements for them. Services include financial health checks, reconciling accounts receivable and payables to the general ledger, inventory batch processing, inventory reconciliations, and more. Virtual Controller also closes a financial skills gap that could have a serious impact on the business by teaching current employees how to analyze what’s happening from a financial perspective, identify areas for improvement, and uncover issues that may need correction. A Virtual Controller consultant can be used on an interim or continuous basis to handle routine financial tasks for manufacturers impacted by the labor shortage.
Some of our customers take a different approach by hiring an outsourced CFO on a temporary basis. The CFO ensures the books are in order at the end of each month and devotes time to training financial employees on various processes. Whether using Virtual Controller or an interim CFO, having a financial gamechanger helps manufacturers do more with less.
3. Managing ongoing supply chain issues.
International supply chains for manufacturing showed a welcome uptick in stability during 2023. Yet, the global supply chain system will continue to face problems in 2024, ranging from unsettled operations and unpredictable global events to smaller trade networks and new oceanic trade routes that can take longer to ship goods and materials.
In this environment, manufacturers should expect continued difficulties when planning around uncertain lead times, job scheduling, and customer delivery times. Electric Power Design (EPD), an engineer-to order manufacturer of power systems to efficiently manage energy supplies, has found a workable solution.
With years of experience finding new ways to provide what customers need, EPD uses the Inventory ERP application to enable engineers to design around existing inventory and offer equivalent products that may have a small change. When EPD doesn’t have the materials on hand to make the product customers want, engineers develop new product lines as a workaround.
The key is having an Inventory ERP application that provides real-time information to keep material counts accurate and up to date and creates forecasts for purchased and manufactured parts. The Planning & Scheduling ERP application helps accomplish this by performing material capacity planning to avoid overuse of excess inventory that could affect jobs already in the schedule.
This approach may not work well for small manufacturers that make the same products over and over. However, whether or not you have the expertise and equipment to make similar parts from excess inventory, knowing what you have in inventory and how much plays a vital role in managing the challenges of global supply shortages.
4. Increasing efficiency with automation.
With lead times for customers getting shorter, using ERP software to automate time-consuming manual processes can drive high efficiency rates that make it easier to deliver jobs on schedule. For years, Cardinal Systems, a manufacturer of custom pool products, struggled to create work orders, perform inventory counts, and other basic production tasks in a timely and efficient manner. Recording actual labor and material costs, managing inventory effectively, and capturing shop floor data in a timely manner also presented major problems.
To overcome these challenges, Cardinal Systems upgraded to an advanced ERP software system and set their sights on automating as many processes as possible. They began by installing 15 Shop Floor Data Collection stations on the shop floor. Workers now digitally log on to work orders and job sequences and the application tracks all labor time as it happens. Labor costs are captured down to the penny in real time.
Instead of spending time trying to locate manual work orders, shop floor personnel can access them in just seconds via the data collection screens. They also use Paperless software built into the ERP system to execute material transactions in real time from anywhere in the shop. Production moves faster and jobs are completed on time for delivery.
Other automated processes that play a key role in high efficiency rates include scheduling, purchasing, inventory management, work order generation, employee messaging, and more. Don’t let manual processes slow you down when these features are available in one integrated ERP system.
5. Getting the most out of your ERP system.
When used to its full extent, ERP becomes the most important asset for manufacturing businesses. Yet, continually improving a company’s ERP skills and capabilities can be difficult to achieve due to human nature. Over time, employees can develop a habit of doing things a certain way, and often resist the need for upgrades or new features. Long-term ERP personnel may retire or move to another company. After a while, processes aren’t as efficient as they need to be. You may recognize those that need improving but aren’t sure how to go about it.
One solution involves hiring an ERP consultant to conduct an audit of production processes. The consultant creates a flow chart that categorizes each process as good, needing improvement, or needing reimplementation and/or retraining. If you agree with the diagnosis, the consultant can provide coaching, training and strategy development to upgrade ERP skills throughout your shop.
However, if the consultant isn’t an expert with your ERP system, you may not get the results you want. It’s one thing to identify inefficient processes. It’s another to teach people how to use ERP differently to achieve the desired results. To help our customers close the gap between where they are now and where they need to be we created a Continuous Improvement Team consisting of our most experienced ERP software, manufacturing, and technology experts. Dedicated to continuously improving manufacturing processes, the team provides the following professional services to significantly improve the use of ERP and maximize your ROI:
- Financial and Operations health checks
- On-site consulting for topics specific to you
- GAP Analysis Process Review to better your operations
- Process Audit to identify areas needing improvement
One of our customers had a slow and cumbersome procedure for manually inputting vendor invoices into its ERP. A Continuous Improvement consultant audited the process and recommended an AI product. Now, when a vendor emails an invoice, ERP automatically matches the PO, receipt and AP invoice with no human input, saving 10 hours a week of dull work nobody wants to do.
The continuous improvement approach is very effective with small to mid-size companies that lack sufficient manpower or the expertise to analyze and improve their processes. Given the rapid advances in ERP capabilities, we recommend manufacturers have this audit performed every three to four years.
With the right ERP, processes and partners, these manufacturing challenges don’t have to derail you. If you’re ready to overcome any of these challenges, we’re here to help.