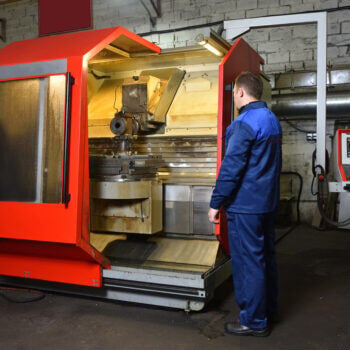
Productivity plays an important role in the profitability and competitiveness of manufacturers by measuring the rate of output per unit of output. When productivity is high it can improve customer service, decrease operational costs, boost employee morale, and help the business achieve its financial goals.
Maintaining high productivity levels is similar to achieving consistent product quality by requiring close and ongoing scrutiny to achieve the best results. Market-leading productivity can be achieved by testing and defining workflows, simplifying material ordering, ongoing training for employees, regular maintenance of machinery and equipment, and identifying bottlenecks on the shop floor.
What sometimes gets overlooked is the ability to improve productivity using ERP software. Our promise is we simplify your manufacturing, and one of the ways we do that is by adding features and capabilities to our ERP system that drive continuous improvement of shop floor productivity. Here are four ways manufacturers use ERP to maintain productivity levels that exceed their competitors.
1. Automate to Do More With Less
Efficiency, defined as “achieving maximum productivity with minimum wasted effort or expense,” is the driving force behind productivity. In the manufacturing world, doing more with less involves producing the same amount of work, or more, with less people.
For years, we have been adding features to our ERP software that can generate efficiencies and simplify processes with less headcount. Here’s an example of how automating manual processes can boost your productivity.
Connecticut Spring & Stamping (CSS), an international manufacturer of precision springs and metal solutions, needed to resolve inefficient processes hampering on-time delivery. After going live with Global Shop Solutions ERP software, CSS experienced improved inventory management and scheduling, particularly when they implemented automated processes.
Manually scheduling with spreadsheets and hand-written charts is about as inefficient as it gets. The time and personnel required to schedule new jobs or reschedule existing ones can take hours or even days, increasing labor costs and reducing efficiency. With the Advanced Planning & Scheduling application, CSS now schedules more than 600 workcenters efficiently and accurately by automating the entire process. This resulted in a 35% improvement for on-time delivery, a 50% increase in sales, and far fewer scheduling-related headaches.
2. Integrate With Third-Party Software
In addition to great ERP, seamlessly integrating your ERP with third-party applications to conduct processes in a fraction of the time it takes to manually perform them will jumpstart your productivity. A highly popular integration for manufacturers is a Nesting Interface software, which saves time and reduces material and labor costs by designing the layout for a piece of metal to be cut most efficiently for different jobs.
The software streams data between your nesting software and your ERP system to determine how many work orders in the queue can fit on your current piece of material from inventory. It then indicates where to make the cuts to optimize material usage, and identifies the leftover material drops and scraps to return to inventory for future jobs.
Another software integration popular among companies that engineer products and build large, complex BOMs is a CAD Interface software. Manually building huge BOMs is a time-consuming, costly process in which mistakes are detrimental. CAD Interface software eliminates laborious data entry by importing the BOM directly from the customer’s CAD software to your ERP. It also speeds production by comparing the imported BOM to current inventory levels in the ERP software to determine if the needed materials are available.
Compac Furniture, which manufactures fully assembled bedroom furniture, uses a CAD/CAM software program to design and build its products. With a wide variety of options available, its BOMs can require up to 30 or 40 lines with many levels on each line. Prior to implementing our CAD Interface software, building their BOMs required planners to export all part information from the design program into an Excel spreadsheet. Before starting production, they had to import the information back into their ERP system piece-by-piece.
Compac Furniture now imports all part information into their ERP directly from the design program. Instead of having to laboriously build each BOM, the CAD Interface builds them, resulting in enormous time savings and increased accuracy.
3. Go Digital For Inventory and Material Movement
Poor inventory management has more impact on productivity than any process, with the exception of scheduling. Counting inventory by hand is rife with human error, such as inaccurate counts, under- or over-purchasing, and difficulty tracking bin, lot, heat and serial numbers for required certifications. These and other inventory roadblocks can cause all kinds of disruptions that slow production and disrupt schedules.
The Inventory application automatically tracks every aspect of your material needs to achieve accurate physical inventory, while controlling material availability and costs. And it does it in real time, so your inventory counts are always up to date. With this software you can:
- Eliminate manual inventory counts
- Automate inventory processes
- Manage materials with multi-location inventory, usage reports, cycle counting and product lines
- Set up automated purchasing based on material requirements, planning functions, and purchase history
- Precisely track inventory data, including bin, lot, heat and serial numbers
- Determine the precise inventory status of multi-level BOMs
- Conduct cycle counting faster and more accurately
- Automatically enter received materials with barcode tracking
Michigan State Industries (MSI) is a manufacturer that provides work opportunities for prison inmates in 13 industry operations. Its old legacy system had no automation, which required all shop floor data to be back flushed. When creating work orders to issue raw material to the jobs, managers had no way of knowing what inventory was already in process until after the work order for each job was closed.
Now they use barcoded inventory transactions to capture inventory and material movement as soon as it happens. No back flushing and no errors from manual data transfer. The software automatically tracks and records the information previously captured on paper or spreadsheets, and the real-time data is available to anyone with access to the shop floor ERP workstations. As a result, managers know the location of every part or material in inventory and where it’s going next.
4. Anytime, Anywhere Raw Material Movement
Manual tracking of raw material movement has long reduced efficiency and productivity. Many manufacturers simplify the process by using GS Mobile, a Paperless software built into the ERP system that executes material transactions in real time from anywhere in the shop. The software is part of a system that redefines the material management process in your facility by using barcode scanning, handheld wireless devices, and radio frequency identification (RFID).
With GS Mobile you can:
- Enter transactions directly from the floor
- Quickly locate parts and materials using a handheld device
- Enter transactions from anywhere in the plan
- Eliminate data entry errors with bar-coded labels
- Perform faster inventory and cycle counting
- Customize transactions
- Increase data accuracy
GS Mobile also facilitates seamless bin-to-bin transfers by scanning the barcode label on the bin where you pull the part. Scan again when you place the part in a different bin and you’re done. You can label materials picked to WIP by printing a transactional issue-to-work order label. Even shipping is faster and more efficient. Scanning and validating as you pull a product out of inventory ensures shipment of the right product and quantity.
At Cardinal Systems, a manufacturer of custom swimming pool products, manual inventory counts used to take two and a half days. With GS Mobile it takes six to eight hours at most, reducing labor costs and providing accounting and senior management with information to make better decisions.
Take Our Manufacturing Health Test
Productivity improvement starts with identifying the shop floor processes that need improving. This Manufacturing Health Test asks questions to uncover roadblocks to better your productivity in eight key areas:
- Performance
- Job Costing
- Scheduling
- Inventory
- Quality
- Labor
- Sales
- Customization
Answering the questions only takes 10 minutes. The test scores your answers and assigns a grade from A to F to identify the areas requiring the most improvement. Then we’ll show you how our ERP software can take you from where you are now to where you need to be.